What Would Happen If We Don’t Do Wire Rope Lubrication?
Wire ropes are crucial components in many lifting, hoisting and pulling applications. They rely on regular lubrication to minimize friction and wear. But what exactly happens if wire rope lubrication is neglected? As per experts like Viper Wrl, the consequences can be severe. Understanding why proper lubrication is vital and how lack of lubrication damages ropes demonstrates the importance of diligent maintenance. Let’s overview the problems awaiting wire ropes that don’t receive adequate lubrication.
Accelerated Abrasion and Wear
Lubrication forms a protective barrier between the steel wires and strands as the rope flexes and moves. This prevents the metal surfaces from grinding against each other. Without lubricant, abrasive wear accelerates. The wires will quickly degrade from the friction and pressure of continuous dynamic bending stress. Wear escalates damage even further. The rope rapidly deteriorates from the inside out.
Increased Risk of Corrosion
In addition to minimizing wear, lubricants also displace moisture from the rope’s core while providing a level of waterproofing. Deprived of lubricant, internal condensation and external water penetration leads to corrosion. Water allows corrosive reactions between the wire and water that produces oxidation, rust and pitting. The rope will corrode from the inside out leading to structural integrity loss.
Loss of Strength and Elasticity
As individual wires wear down, bend and corrode, the rope loses strength capacity and elasticity. Yield strength declines. The outer strands show kinks and flattening from fatigue.
Permanent stretching and deformation occurs more easily under loads. The inner core compactness loosens. The rope cannot equal a well-lubricated rope’s dynamic load ratings.
Binding and Seizing
Without lubricant, friction can cause individual wires and strands to temporarily stick and bind during operation rather than sliding smoothly. This impedes function. In extreme cases, unlubricated ropes may seize up entirely, bringing mechanical functions to a halt. The rope gets damaged internally from forced binding and tugging.
Jamming and Clogging
Lack of lubricant also allows grit, dirt and grime to build up both externally and internally on the rope. Dust and particles can clog between the strands. This gradual contamination interferes with smooth wire and strand interaction. The rough particles exacerbate abrasion. As sludge builds up, the rope cannot function properly.
Inflexibility and Stiffness
Ropes deprived of lubricant lose flexibility from escalated wear and fatigue. The wire strands compact rather than gliding fluidly. The rope feels stiff. Inflexibility reduces mechanical efficiency. The rope strains to bend and conforms less effectively to sheaves and pulleys. Fatigue is cut short.
Excessive Heat Generation
Without lubricant, the friction and strain on the rope creates internal heat buildup. This added heat accelerates wear effects even further. In extreme cases, unlubricated ropes under load can overheat severely, causing deformation and structural damage. Rope life is significantly shortened.
Premature Failure and Breakage
The combined effects of wear, corrosion, fatigue, contamination and internal load imbalance caused by lack of lubrication lead to premature failure. The rope deteriorates from the inside out. Failures may occur as broken wires that propagate or complete snap. Sudden failures compromise safety.
Conclusion
Regular rope lubrication is crucial to slowing deterioration and extending service life. Don’t wait until problems occur – prevent them entirely through proper maintenance.

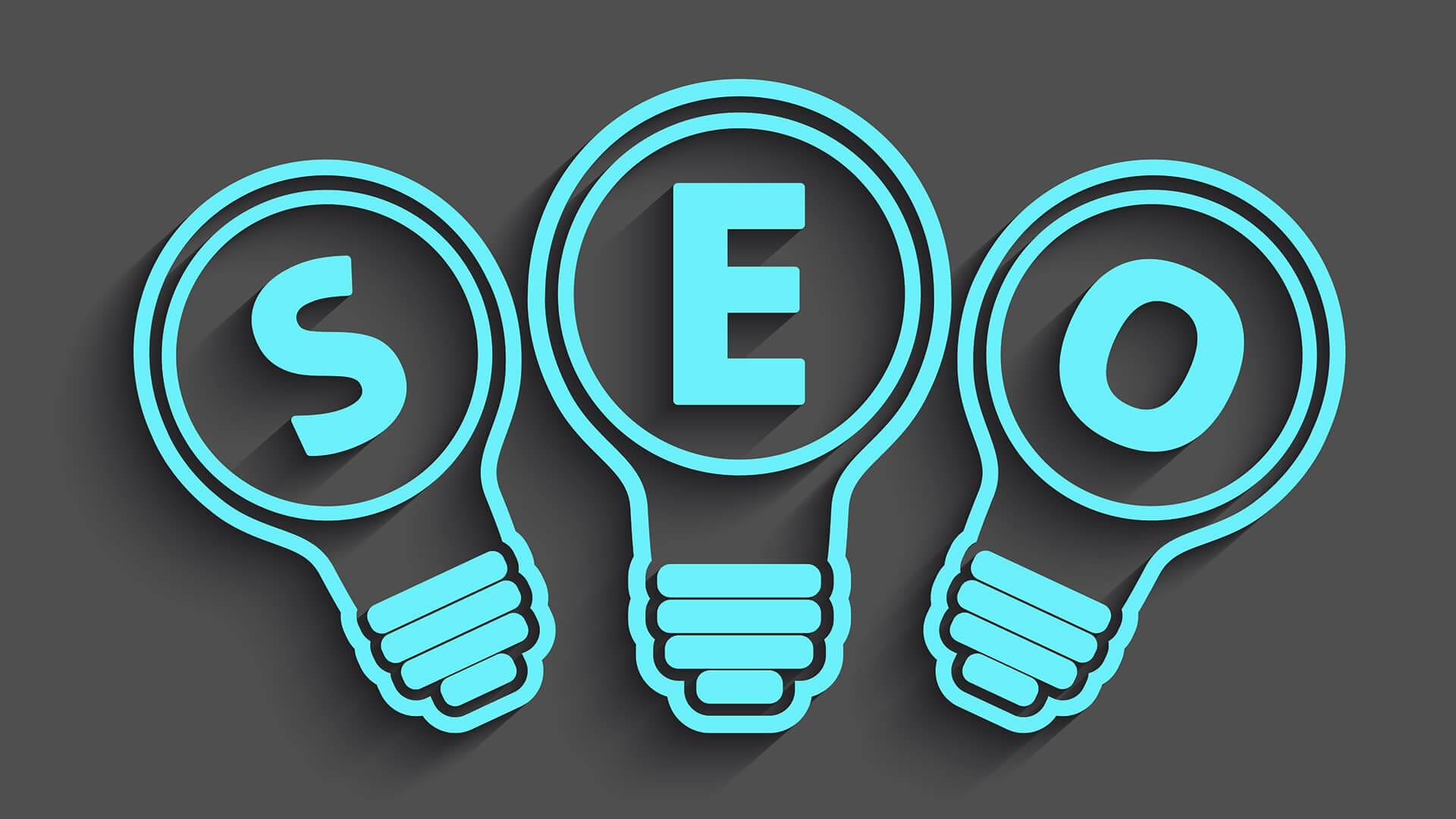
3 Comments
heather
I love learning new things every sigle day and this I didn’t know about. Sounds like this process prevents a lot of accidents.
Terri Quick
Thank you for sharing this
Tamra Phelps
Well, I didn’t even know about this, so I would have never known to lubricate them, lol. Good to know,